How to Bypass Frame Slop Error on 5 Pin Rotary with Switch on older Thunder Laser Machines
Preface: This article is for those users with older machines that have a 5 Pin rotary with a switch and are using Lightburn. Your rotary is driven by the Y axis output and not the U Axis output.
Background:
Older Thunder Laser machines used the Y axis driver outputs from the controller to control the rotary where as new machines use the separate U Axis driver outputs. So on the older machines, the Y Axis limits appear to cause issues with Frame Slop errors even though a rotary is plugged in. It will be most prevalent on the smaller machines like the Nova 24 due to the short Y axis dimension. If your machine is mid 2020 or older, it is likely affected by this.
Things to look for:
If you have a 5 pin rotary port and switch and lack U-Axis wiring, you are affected by this.
5 Pin Rotary and Switch | Controller Lacks U Axis Wiring |
| |
Another clue would be if you send a Job in Absolute Coordinates and do not get the Alarm for it when you try to run the job:
The workaround:


When you have this work around enabled, the Y axis will be allowed to over travel and may run into a hard stop and fault out. It is your responsibility as the operator to take precautions and understand this. Typically to recover a faulted Y Axis you would just need to power cycle the machine. With the wrong value in place, the Frame Slop protection for Y axis is bypassed, so be careful on how you set your origin and how you frame your projects.

If you use a middle type user origin, you may be less likely to experience this issue. If you use a top or bottom origin, you are losing a portion of the bed due to the Rotary being place on the bed somewhere in the middle region.
So in order to be able to process your Tumbler (likely a large Full Wrap or a Dog Bowl/Jug type) you will need to modify the machine settings. Once done, return them back to what they were prior.
Edit Machine Settings | Scroll Down in Machine Settings |
In Lightburn, go to Edit>Machine Settings
| Expand the Vendor Settings Section
Read and then click Yes on the prompt
|
Change Y Axis Max Travel (mm) | Enter a new Value and Write |
Scroll down the Y Axis Settings section. Take note of your stock value for Max Travel (mm) which may be different than what is shown.
| In this example, 1200 was entered for Max Travel (mm) and then the Write button was clicked. Verify that the setting was written by clicking the Read button.
|
At this point, you should set up your rotary project as usual with the proper origin and run it. Once complete and done with the rotary, we need to revert back for flat jobs. Turn off the Rotary enable switch and perform the following steps.
Home the machine to 0,0 | Press Origin Button |
We want to home the machine back to 0 just in case the Y axis has a position value greater than its actual motion range in the flat Y direction would allow. Use the HOME button on the laser window to send the head back to the top left corner of the machine.
| Once the head is at the Home position, press the Origin button to assign the new User Origin.
|
Revert your Y Axis Max Travel (mm) | Press the Reset button to Re-Home |
Follow the steps like you did previously but set your value back to what it was. It may not be the 400mm shown here.
| Have the machine do a Re-Home so that it will know 0,0 and ensure that it will not hit a hard stop when you try to run flats again.
|
Why it happens:

Read this section if you want to get into the nitty gritty of why the Frame Slop error happens and some other insight on how to remedy.
Visual:
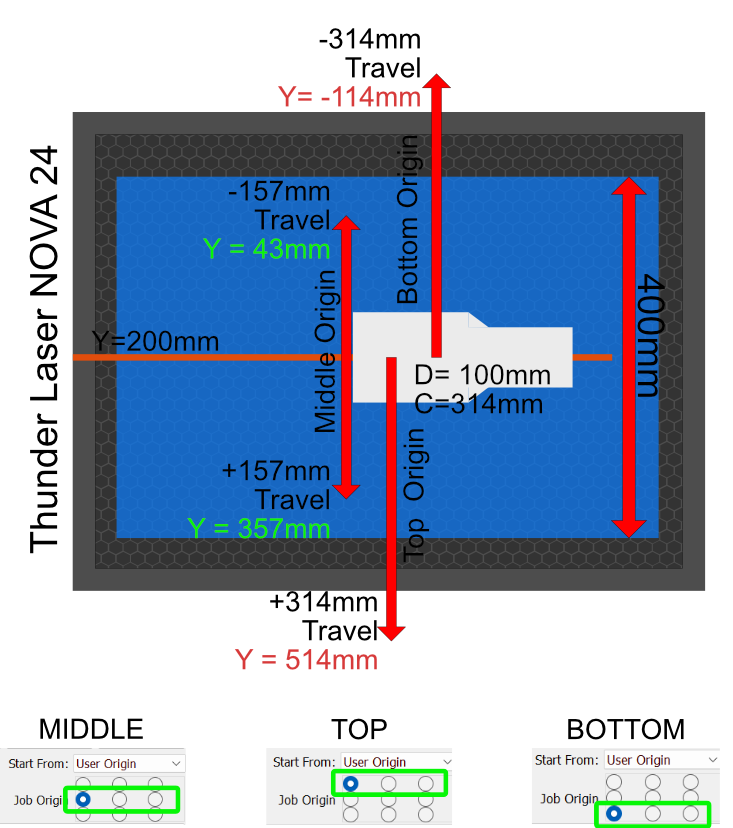
In this example you are using a Nova 24 with 400mm Y axis max travel and a tumbler with a 100mm diameter which is a 314mm circumference. You then place the rotary in the machine, lets say right at the center of the Y axis position, so 200mm. This means you have +- 200mm roughly in each direction. If you use a middle origin, you need half of the Cups circumference to travel up and the other half down (since the controller is using the Y axis, travel is limited to the Y axis limit of 400mm) which is 314mm/2 = 157mm. So that cup should work fine since 157 is less than the +- 200mm of travel that we have.
BUT....if you use a top or bottom origin, you now need the full Tumbler circumference to travel either Up or either Down (depending on whether you chose Top or if you chose Bottom), so now we need the full 314mm of travel which is greater than the +-200mm that we have available. This will result in a Frame Slop error.
Now...depending on where you place the rotary, you may be able to get +300mm and -100mm travel or +250mm and -150mm and so on. Which can lead to "well it worked last time when I ran it but not this time" so keep that in mind.
Reference Articles:
If you are a Thunder Laser USA client and still need Technical Support after exhausting the resources in the Knowledge Base, simply email
support@thunderlaserusa.com and the Technical Support Team will promptly assist you! You can also use the form
here.
Information contained in this Knowledgebase, on this page, in this or any other Article etc. is the property of Thunder Laser USA and shall not be copied, re-used, sold etc. Do not copy, distribute, or reproduce without express written permission from Thunder Laser USA.