Preface: This article covers a sample setup and workflow for a Tumbler on EzCad3 using a Roller Rotary on an Aurora Pro 20W Mopa Fiber Laser. This article assume you know the marking parameters(hatching, power, freq) etc for the tumbler you have.
You will need to bypass the Safety Doors of your Aurora Fiber Laser Machine. In doing so, you accept all liability and release Thunder Laser USA from any issue that may arise from the bypass. You also agree to wear the proper PPE when bypassing the Aurora Machine Safety Doors. Doing the Safety Door bypass is at your own risk.
This workflow is one way to complete a Rotary Job. It does not necessarily mean it is the only way. Each workflow for each type tumbler may vary a little. This article does not cover 2 sided or full wraps either.
This article was written by using Ezcad3 build 1768, if you have a different version you may experience different options and the software may look different
Proper PPE for Operating the Laser with the Doors Bypassed
Flexible Measuring Tape
Metal Ruler
Bubble Level
Focus Gauge (Optional)
Calipers
Painters Tape
Pen\Black Sharpie
Calculator
Consistent value for Pi = 3.14159
Roller Rotary Motor Steps - Default is 4400 for the Rotoboss Jr that was used
Roller Rotary Wheel Diameter - Default is 40mm for the Rotoboss Jr that was used
Tumbler Diameter at Roller Rotary Drive Wheels - Use a Pi Tape to read the value
Setup and workflow Steps:
Step 1: Gather Measurements Listed Above
In this example we have:
Roller Rotary with a 4400 Steps Value
40mm Roller Diameter
Tumbler that is 100mm in diameter
Generate Values that will be used Later On:
Pulses Per Round = (Cup Diameter/Roller Diameter)*Roller Rotary Steps = (100/40)*4400 = 10050
Circumference = pi*diameter = 3.14159*100mm = 314.159mm
Setup the Roller Axis: A
Power up your machine and open up EzCad3, then press the Para[F3] button or Press F3 button on your keyboard to open up the Parameters window
1. Select Axis Solution
2. Select from the drop down to Enable the A axis
3. Set the value for Common Cathode output to True
4. Set the value for Pulses per round to the Value calculated previously, for this example the value is 10050.
5 . Make sure the 4 options for E ncoder Feedback, Home, Limit Switch and Software Limit have the Enable field set to False
6. Click Ok
You should now have additional information displayed at the bottom of EzCad3 which will be for your A Axis Rotary Solution
Setup Split Param:
Click the Split Param. Button in Mark window. The window will initially look like this:
1. Select the A:A axis mode as Y from the drop down menu. Click OK and open the Split Param. Window again.
2. Set the Y:Split Mode to Split by size
3 . Set the Split Size to your desired split size. In this example we used .1mm
4. Click OK
Your Mark window should now look something like this:
Click the Part Diameter button. Enter your tumbler diameter. In this example, we used a 100mm tumbler. Click OK to close the Part Diameter Window
Setup the Door Bypass
You
will need to bypass the Safety Doors of your Aurora Fiber Laser
Machine. In doing so, you accept all liability and release Thunder Laser
USA from any issue that may arise from the bypass. You also agree to
wear the proper PPE when bypassing the Aurora Machine Safety Doors.
Doing the Safety Door bypass is at your own risk.
Press the Para[F3] button in the Work window or Press F3 button on your keyboard to open up the Parameters window
1. Select the Port option
2. For Door IO , set the Active low Level to True
3. Click OK
This will invert the doors so that the machine will run with the Doors Open but not with the Doors close. You must undo this when not using the Rotary
Setup Artwork Basics:
This does not go into the full detail of setting up your artwork like hatching, speed, power, frequency, skewing ETC. It only covers the basics.
Step 3: Setup the Roller Rotary in Machine
Installing Tumbler onto Roller Rotary
Adjusting Focus
You must manually focus the laser head since the surface you are trying to project to is rounded it will be difficult to use the auto focus sensor.

Note that when the rotary is installed and you are adjusting Focus you may get a very loud beep. This is due to the Auto Focus Sensor reading off a point of the Rotary and not the normal bed location. It is warning the the position of the Lens is "out of range" because it believes the lens is too close. One way to silence it is to position the rotary so that the Red Dot Auto Focus spot can reach the aluminum bed plate or to place your hand over where the Red Dot Auto Focus Spot is pointing on the rotary and do a slight "Bump" up\down adjustment.
Focus Method 1: Measure Distance to Head
Focal Distance to Lens:
Focal Distance to Galvo Head Red Dot Focus Sensor:
For this test we are using the F-210 Lens so we will target 9.5" to the lens or 10.83" to the Galvo Head Red Dot
Method 2: Visually view Red dot Trace Line Width
1. Draw a 30mm line on a piece of painters tape with a black Sharpie and Metal Ruler.
2. Use Ezcad3 to Draw a Rectangular contour 30x1mm and then use the Up/Down Arrows to adjust the projection until the line you drew on the painters tape is encompassed by the red tracer. You will need to move the tape to the red tracer as you adjust Focus Height. After completing this test I measured ~9.5" to the lens.
Step 4: Test the Setup Configuration
Test Spin the Cup and Adjust Settings
Origin Setup
Step 5: Burn the Cup
Start the Job
Step 6: Return EzCad3 to Previous Configuration
Disable the Safety Door Bypass
Press the Para[F3] button or Press F3 button on your keyboard to open up the Parameters window
1. Select the Port option
2. For Door IO , set the Active low Level to False
3. Click Ok
Disable the A Axis for Roller Rotary
Press the Para[F3] button or Press F3 button on your keyboard to open up the Parameters window
1. Select the Axis Solution option
2. For Axis Solution , set the Axis solution to NONE
3. Click Ok
Videos:
Additional Things to Note:
Understanding the A Axis Control Window
1. Part Diameter = Enter your Part Diameter
2. Split Param = Split Parameters control window button
3. Current Position of Rotary in MM (simulated Y Axis position)
4. Buttons that will Jog the rotary by the value set in Item 5
5. Distance to Jog the rotary with the arrows in item 4
6. Go buttons to send the rotary to the Set Origin or Special Position (Akin to User origin)
7. Button to open the Set Origin window
8. Value of Origin Position of Y Axis in MM (Note that when setting an origin, it is done for the A Axis so it is entered in degrees). This value relies on the information input to Part Diameter item 1
9. Button to Assign Current Y Position to the Special Position(Akin to User Origin but used as repeatable Location)
10. Value of the Special Position in mm of Y Axis in MM
11. Artwork Projection to show Skew
12. Calculates Work Preview to show Split Marking Setting
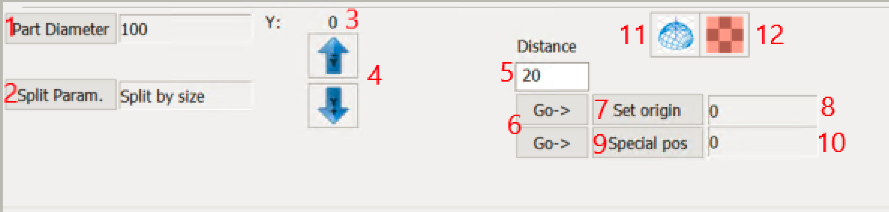